Hey guys, Joe Paisans here with advanced innovation. I want to say thank you to everybody that continues to subscribe, comment, and leave me thumbs up on awesome videos. A couple of videos back, I showed you how to precision indicate a part in a three jaw Chuck. The primary objective of that video was to tell you that you must establish square before you establish concentricity. It was very important and I got a lot of feedback on that one. Many people mentioned that they don't have an adjustable Chuck, so even if they can get the part to run square with the machine, it's still out of concentricity. Today, I'm going to show you that no matter how bad your lathe is, you can get a part to run fairly true if you take your time and do a little bit of homework. Alright, let's take a walk over to the machine. I'm going to reposition the camera and show you how to make it happen. First thing I'm going to do is throw the Chuck body as far off the center as possible. I'm going to look for a continuous surface to do that, and right behind the jaws is usually a good place. Let's set the indicator in there and see what we got. My Chuck body is about half a tooth out. I'm going to loosen up all my adjusting screws. I'm going to tighten screw number 1 and then go to screw number 3, making sure it's not making contact. Once I tighten it down, I'll do the same thing with screws 2 and 4. That will pull it in a small diagonal. I'll snug screw 3 to prevent it from coming out and bump screw 4 to keep it in place. Now let's...
Award-winning PDF software
Video instructions and help with filling out and completing How Form 8815 Adjusted
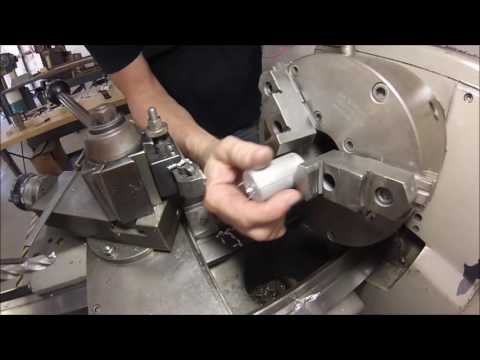