Hello, I'm Cash from Cashed Out Boards. In this video, I will be providing a complete guide to making a longboard. Let's get started! The first step in making your own longboard is planning out the board. For my board, I decided on a size of 10 inches by 38 inches. It will be symmetrical and have kicks and concave. Once you have the shape and size in mind, you can begin marking out your materials. I will be using 4 plies of eighth-inch Baltic birch plywood. It is important to use a square or straight edge to ensure precision while marking the plywood. Keep in mind that Baltic birch plywood is flexible in one direction and rigid in the other. After marking the materials, it's time to cut out the sheets of plywood. I recommend using a circular saw for this step. Remember to clamp down the plywood and wear safety glasses. Now that you have the plywood cut out, you will need to make a press to turn the wood into a longboard. Find a sturdy board slightly longer and wider than the desired longboard. Additionally, find long, skinny strips of wood for concave and kick tails. Create a clamping system using four two-by-fours, threaded metal rods, nuts, and washers. Smooth the ends of the rods with a grinder to prevent cuts. Drill holes at each end of the two-by-fours, slightly larger than the thickness of the rods. Assemble the clamping system with nuts and washers. Next, prepare for gluing by cutting some cardboard spreaders and obtaining wood glue. I recommend using Tightbond II or III. Set up the concave and kick tail shim and place the first sheet of plywood on it. Spread a generous amount of glue evenly on the plywood, making sure to cover the edges. Have someone assist you...
Award-winning PDF software
Video instructions and help with filling out and completing What Form 8815 Cashed
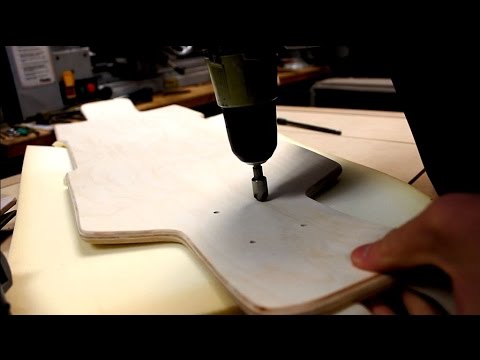